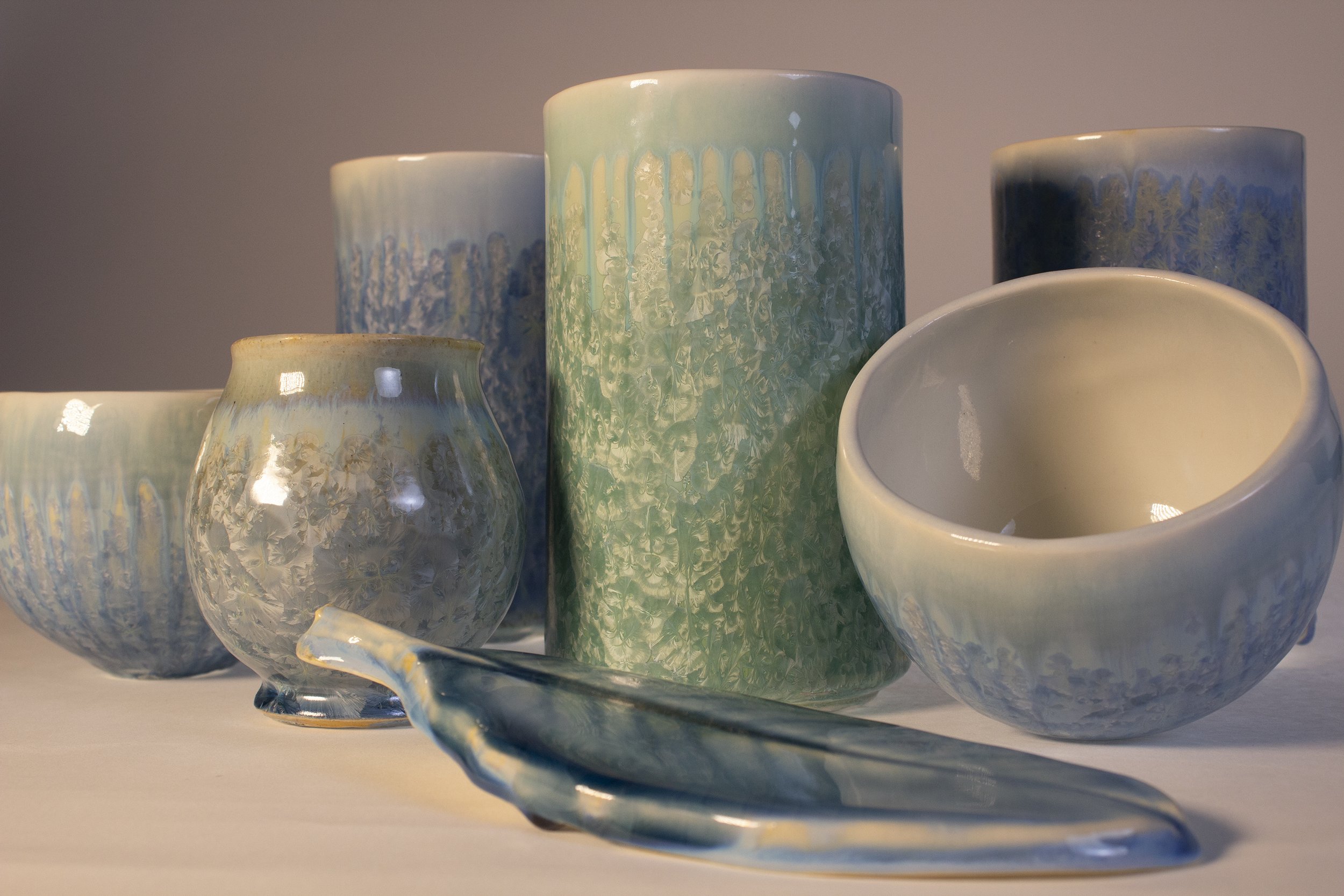
In Spring of 2022 I started experimenting with copper carbonite and cobalt carbonate cone 6-8 crystalline glazes on slipcast porcelain and thrown stoneware. I tried to thread the needle between the flux necessary for crystal development and the arduous and dangerous work of post-processing.
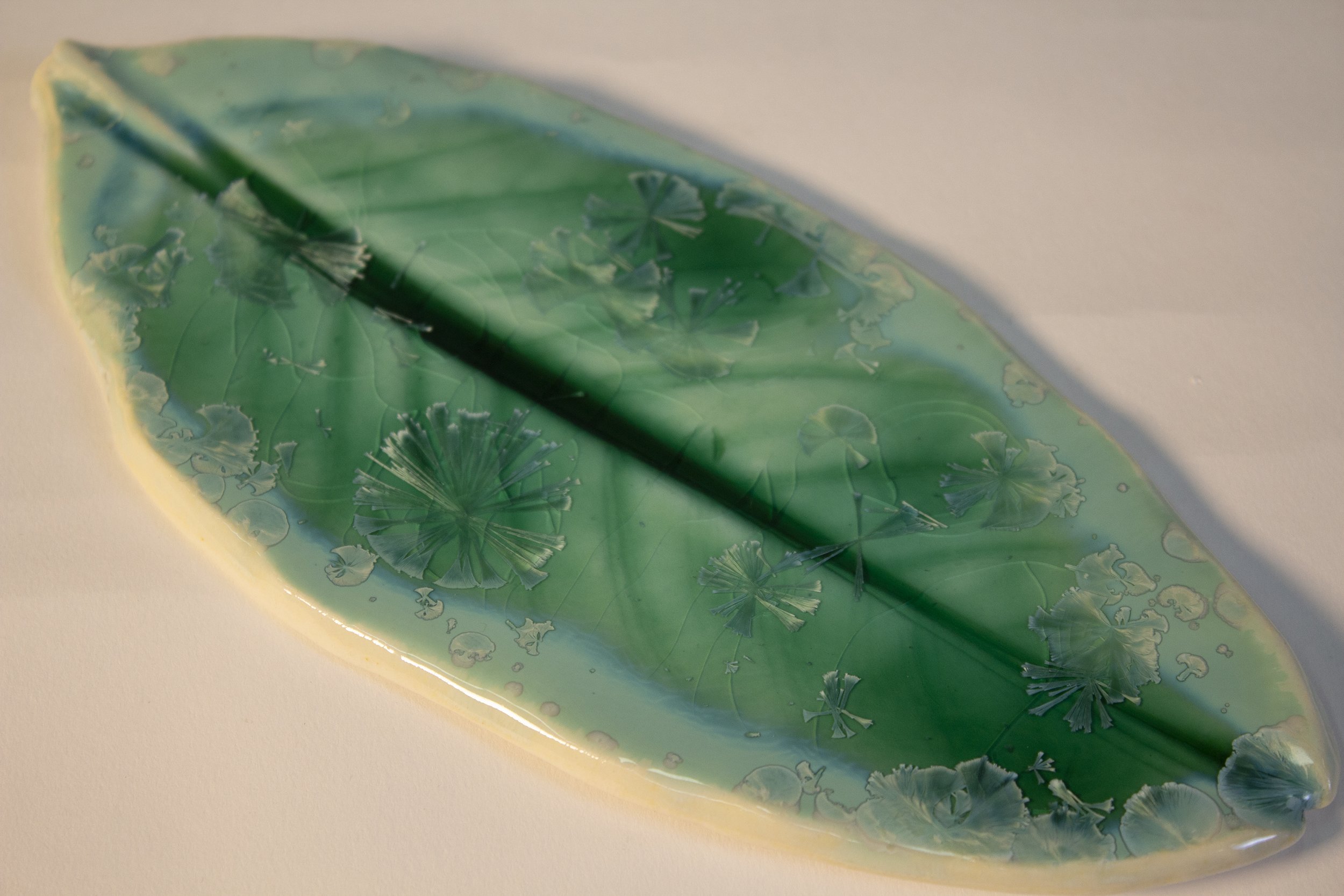
I found that when fired flat, I could achieve blooming crystals in the foreground against deep, jewel-like pools in the background

When using a white gloss liner glaze, it inhibited all crystal growth, but produced a beautiful, soft feathering.

In Spring of 2023 I attempted to use physics instead of chemistry to control glaze flow. I 3D-modeled, 3D-printed, and then cast these testers with a high amplitude foot design, hoping to use surface tension to stop the flow of glaze at the bottom of the piece.
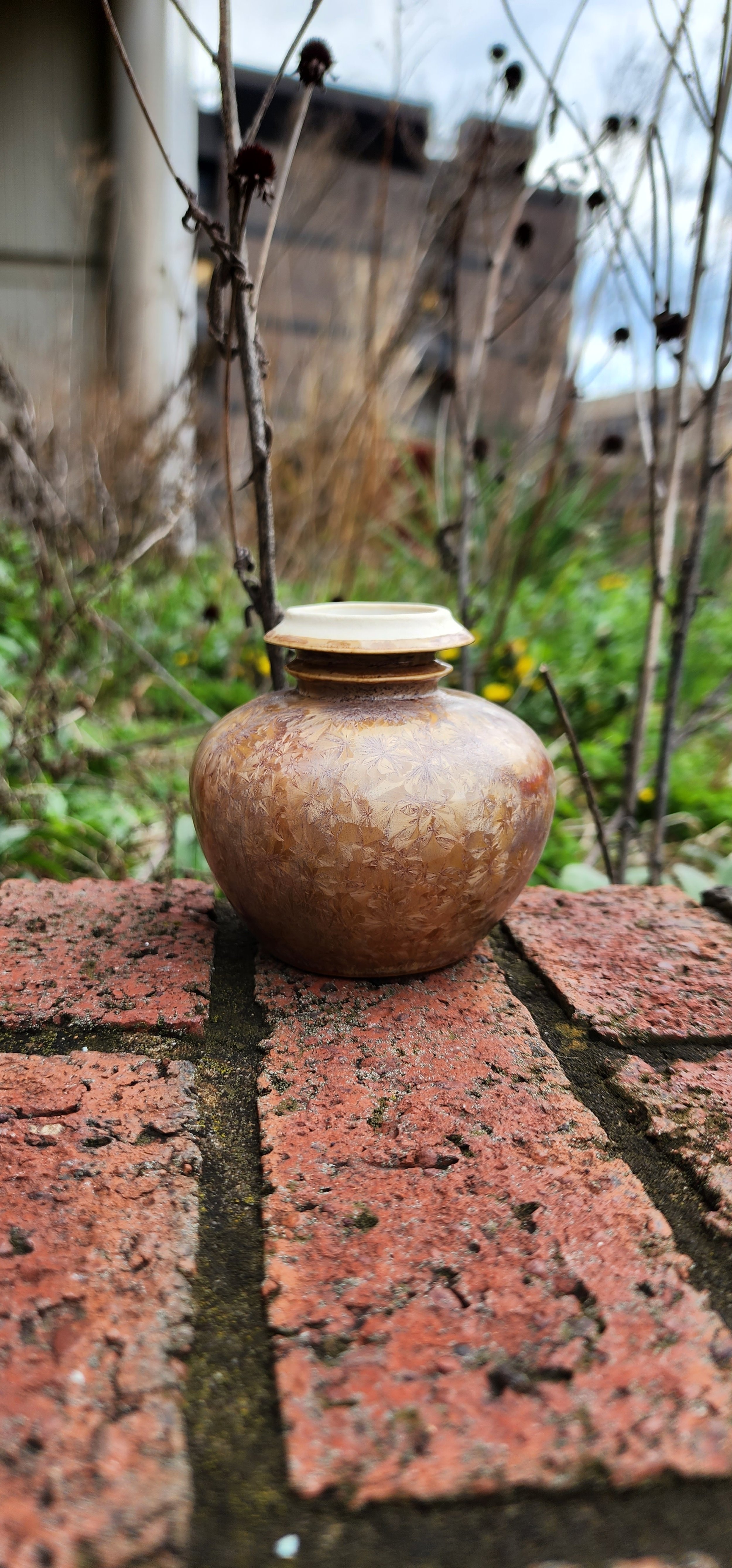
As seen with a manganese carbonate crystal, it was incredibly effective. As a bonus, these little testers could be inverted for sale as bud vases, ink pots, fluid containers, etc. People loved them, and it meant a lot to me that I wasn’t just producing ceramic garbage; Every piece, even the testers, were complete, functional works.

This is my second high-amplitude foot design, a small vase shown here in my manganese dioxide glaze. Neither the tester bud vases or these larger vessels required firing rings, boats, pedestals, or any kind of post-processing, dramatically cutting down prep time, finishing time, and risk of injury on a crystalline piece.

As seen in this nickle crystalline, periodically the high-amplitude foot worked unpredictably, leaving bald spots at the narrowest points where glaze pulled into legs during firing and away from the surface.

The bowls, like this one in manganese carbonate, continued to require firing rings, boats, and grinding.
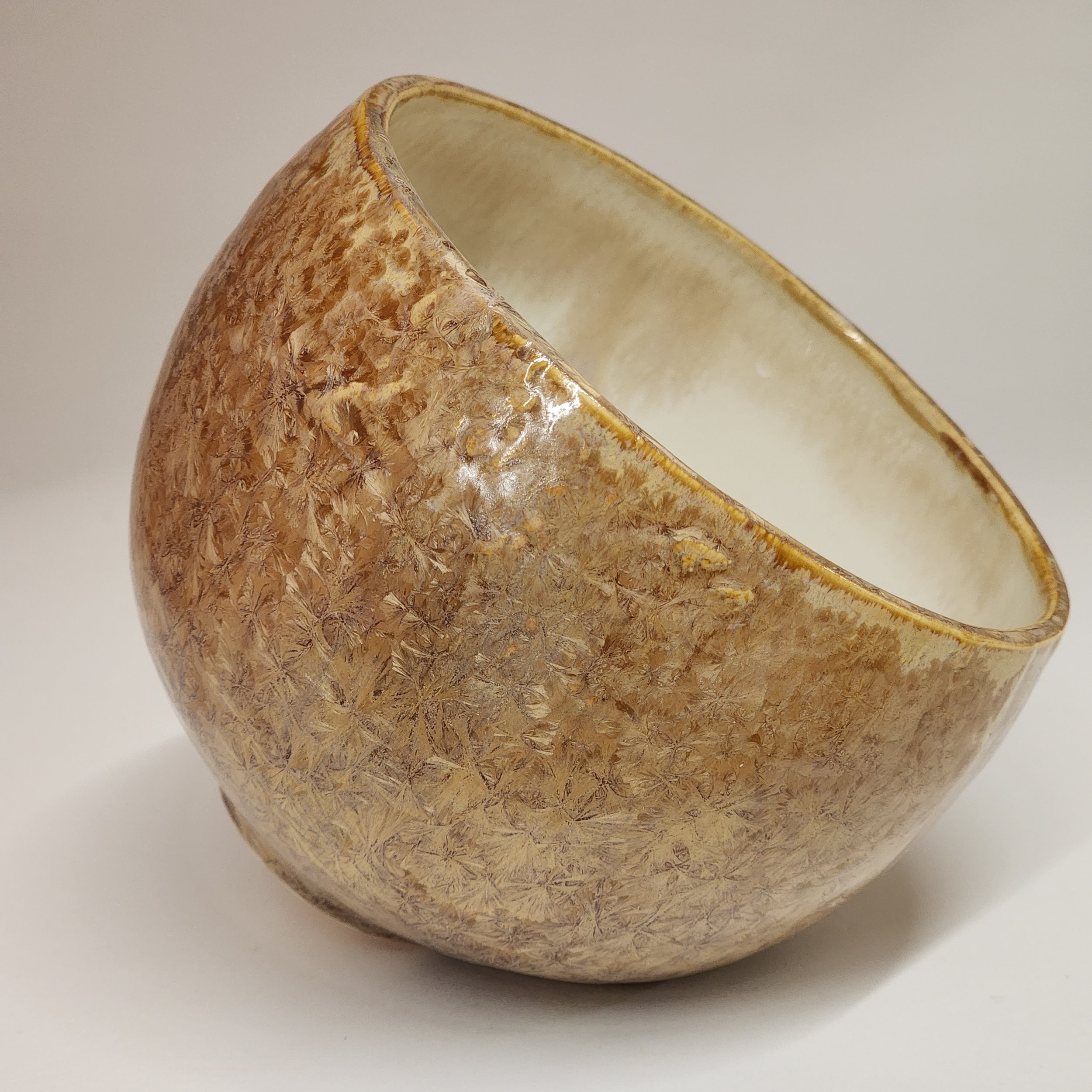
Overseeding remained an issue, but honestly, I'm kind of into it.

We attempted a standard ^6 with no firing schedule in a different kiln to see if we could mitigate the overseeding. We weren’t successful in producing a real crystal, but people still seemed to like these really tactile finishes

They liked them so much, in fact, that another artist, Connor Taylor, offered to custom-make wooden stands for them out of wood chosen specifically to bring out the colors in the glazes.

An unexpected benefit of firing the tester bud vases upside down is the stunning crystal formations on the bottoms of the pieces. When in use these are kept a kind of secret, and I enjoy sending these pieces home with patrons knowing they have something that will always be fascinating.
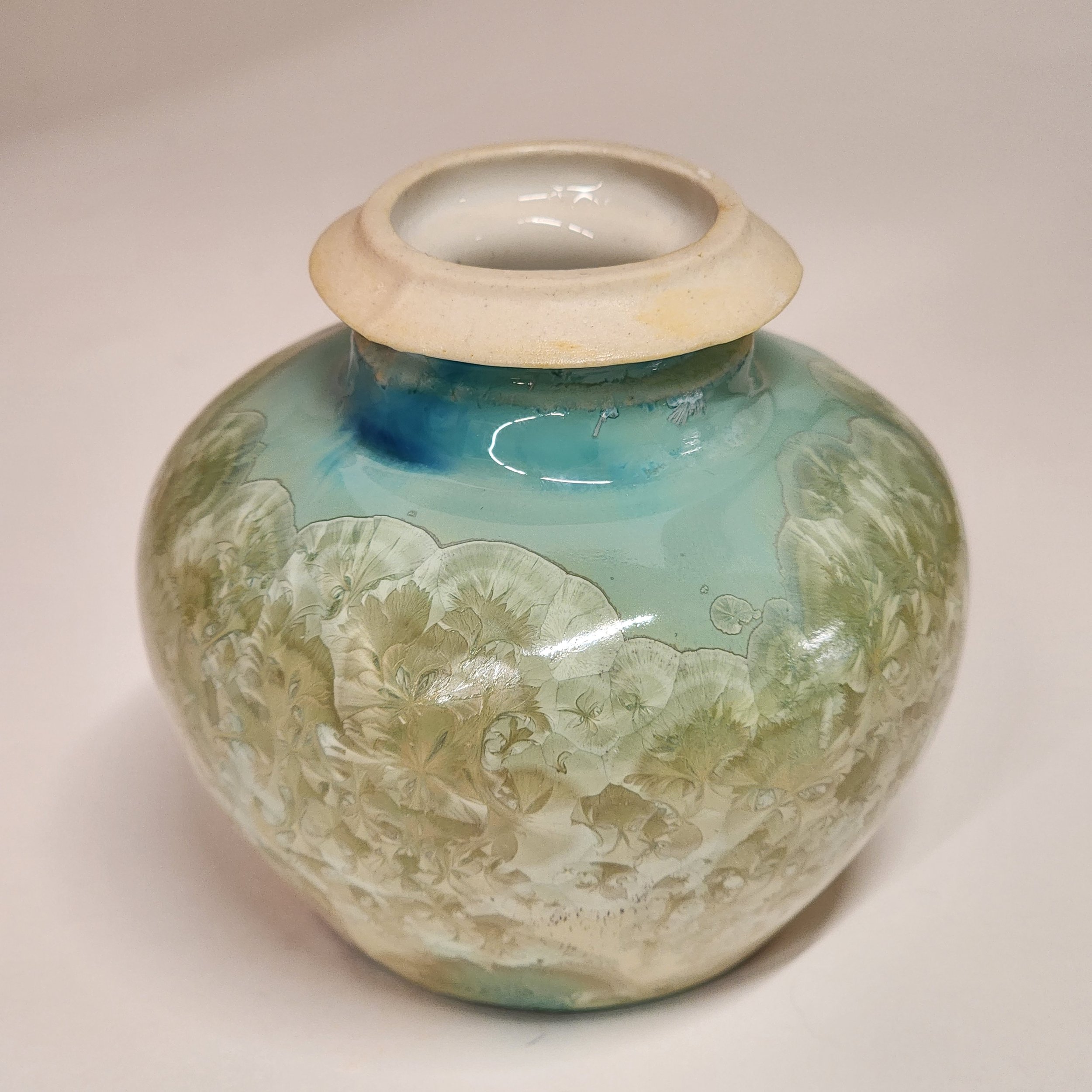